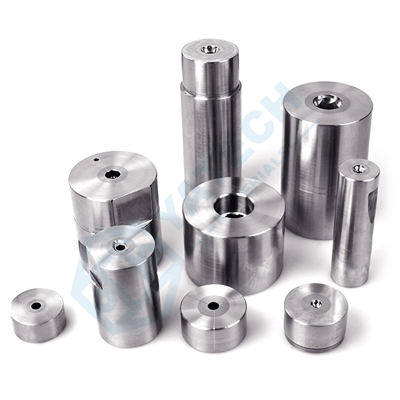
Soğuk başlık kalıbı malzeme gereksinimleri ve seçimi
- Performans gereksinimleri soğuk başlık kalıp malzemeleri
Standart bağlantı elemanı endüstrisinde, soğuk başlık kalıpları soğuk başlık deformasyon işlemi sırasında büyük bir birim basınca dayanmak zorundadır. Deformasyon derecesi büyük ve malzeme sertliği yüksek olduğunda, birim basınç 2.000 MPa'nın üzerine çıkabilir. Aynı zamanda, metal şiddetli bir şekilde akar, bu nedenle soğuk başlık kalıbı Kalıbın yüksek basınç altında hasar görmemesi, deforme olmaması ve aşınmaya dayanıklı olması için yüksek mukavemete, iyi yorulma direncine, yüksek sertliğe ve iyi yorulma direncine sahip olması gerekir.
Parçaların doğruluğu.
(1) Yüksek mukavemet.
The soğuk başlık kalıbı 2.000-3.000MPa birim basınç altında plastik deformasyon ve çatlama olmaksızın çalışmalıdır.
(2) Daha yüksek tokluk.
Tokluk, özellikle darbe yükü koşulları altında çalışan kalıplar üreten kalıp çeliği için kalıp çeliği için önemli bir performans endeksidir. Genellikle 50~55HRC'den düşük sertliğe ve yüksek tokluğa sahip kalıp çeliği olarak kullanılır.
(3) İyi yorulma direnci.
Metalin hızlı deformasyonu ve iç sürtünmesi, iş parçasının sıcaklığını 200 °C'nin üzerine çıkarabilir. soğuk başlık kalıbı sertliği değişmeden bu sıcaklıkta uzun süre çalışabilmeli ve sürekli dövülüp ekstrüde edilebilmelidir. Soğuk ve sıcağın dönüşümlü stresine rağmen hala iyi yorulma direncine sahip olabilir.
Yaşamı iyileştirmek için soğuk başlık kalıbı, farklı önlemler alınabilir. Yağlama koşullarının iyileştirilmesi, makul bir şekil tasarlanması gibi soğuk başlık kalıbı, pürüzlülük değerini azaltmak, vb. işleme kalitesini iyileştirmek için soğuk başlık kalıbıÖngerilmeli kombine kalıbın kullanımı kalıbın ömrünü uzatmada çok etkilidir.
Öngerilmeli kombine konkav kalıpların kullanımı aşağıdaki avantajlara sahiptir:
a.Kalıp mukavemetini artırın. İlgili bilgilere göre, iki katmanlı kompozit kalıbın mukavemeti genel kalıbın mukavemetinin 1,3 katıdır ve üç katmanlı kompozit kalıp genel kalıbın mukavemetinin 1,8 katıdır (belirli bir kalıp boyutu için).
b.Kalıp çeliğini koruyun. Orijinal genel kalıp tamamen kalıp çeliğinden yapılmıştır Üretim, şimdi iç halka boyutu küçültülmüştür, dış halka alaşımlı çelikten veya orta karbonlu çelikten yapılabilir.
c.Kalıp boyutunun küçültülmesi nedeniyle ısıl işlem işlemi kolaylaşır ve ısıl işlem kalitesi artırılabilir.
d.Kalıp hasar gördüğünde sadece iç halkanın değiştirilmesi yeterli olur, öngerilmeli halka tüm kalıbı hurdaya ayırmaya gerek kalmadan kullanılabilir.
Öngerilmeli kombine kalıp kullanımının bazı dezavantajları da vardır: işleme yüzeyinin artması, yüksek işleme teknolojisi gereksinimi gibi.
- Kalıp malzemesinin seçimi
2.1 Özellikleri sementit karbür kalıp malzemeleri
Çimentolu karbür, orta ve iri taneli nadir refrakter karbürlerden (tungsten karbür veya titanyum karbür) ve bağlayıcı olarak metal kobalttan oluşur ve kalıp çimentolu karbür olarak kullanılır, bunların arasında nadir refrakter karbürler genellikle karbonize edilir. Tungsten. Toz metalurjisi yöntemi nedeniyle, bu alaşım hala tungsten karbürün orijinal özelliklerini korur, sertliği elmasa yakındır ve aynı zamanda bağlayıcı olarak kobalt nedeniyle tokluğa sahiptir.
Karbür kalıbın aşağıdaki avantajları vardır:
(1) Yüksek aşınma direnci. Sinterlenmiş karbür kalıp malzemesi yüksek aşınma direncine sahiptir, bu da kalıbın herhangi bir deformasyon derecesi altında uzun süre çalışmasını ve standart parçaların boyutunun değişmeden kalmasını sağlayabilir.
(2) Mükemmel cilalanabilirlik. Çimentolu karbür iyi cilalama özelliklerine sahiptir ve çalışma yüzeyi, standart parçaların yüzeyinin yüksek kalitesini sağlamak için ayna yüzeyine cilalanabilir.
(3) Metale düşük yapışma. Soğuk başlık işlemi sırasında, demirli metal malzeme, çimentolu karbür kalıp malzemesine düşük yapışma özelliğine sahiptir, bu da çimentolu karbürün yüksek bir hizmet ömrüne sahip olmasını sağlar soğuk başlık kalıbı.
(4) Sürtünme katsayısı küçüktür ve enerji tüketimi küçüktür.
(5) Yüksek ısı iletkenliği. Sinterlenmiş karbür kalıp malzemesinin yüksek ısı iletkenliği sayesinde, soğuk başlık işlemi sırasında oluşan ısı hızla uzaklaştırılabilir ve bu da kalıbın dayanıklılığını artırır.
(6) İyi korozyon direnci. Havaya, aside ve alkaliye karşı mükemmel korozyon direncine sahiptir.
Çünkü çimentolu karbür kalıp malzemesi yukarıdaki özelliklere sahiptir ve çimentolu karbür kompozit kalıp kullanılır, kalıp ömrü genel yapı kalıbının 40 ila 60 katıdır, hatta 200 katına kadar çıkabilir. Bu nedenle çimentolu karbür ucuz ve ideal bir kalıp malzemesidir.
2.2 Çimentolu seçim karbür kaliteleri
Standart parçaların soğuk şekillendirme işleminde, semente karbür kompozit kalıbın büyük bir darbe kuvvetine dayanması gerekir. Kullanım gereksinimlerini karşılamak için, yüksek kobalt içeriğine, yüksek mukavemete ve iyi darbe tokluğuna sahip semente karbür seçmek gerekir. CG5, CA18, CA24 gibi karbür alaşımları.
Şekillendirme Aletleri Boşlukları, Çimentolu karbür bağlantı elemanı kalıp boşlukları
WC Tane Boyutu | Seviye | Co% | Yoğunluk g/cm3 | Sertlik HRA | TRS not ortalaması | Uygulamalar |
Orta | CG5 | 12 | 14.3 | 88.3 | 3300 | Yüksek tokluk soğuk başlık kalıpları |
CG6 | 14 | 14.12 | 87.3 | 3140 | ||
Kaba | CA18 | 18 | 13.75 | 85.1 | 2940 | Φ20'nin altında açıklığa sahip vida kalıbı |
CA24 | 24 | 13.25 | 82.5 | 2650 | Vida kalıbı Φ20 - Φ50 | |
CT15 | 15 | 13.8 | 86 | 2700 | Altta açıklıklı paslanmaz çelik vida kalıbı <Φ2 | |
CT20 | 20 | 13.6 | 84.5 | 2660 | Açıklığı >Φ2'nin üzerinde olan paslanmaz çelik vida kalıbı | |
CA20 | 20 | 13.55 | 84.1 | 2740 | Sıcak/sıcak dövme kalıpları |
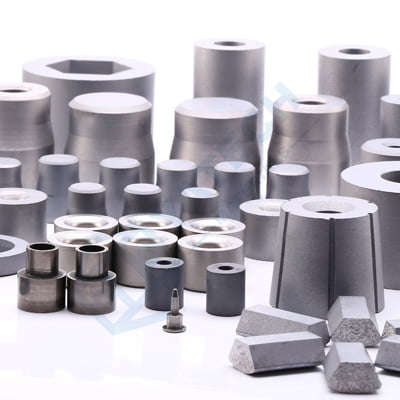