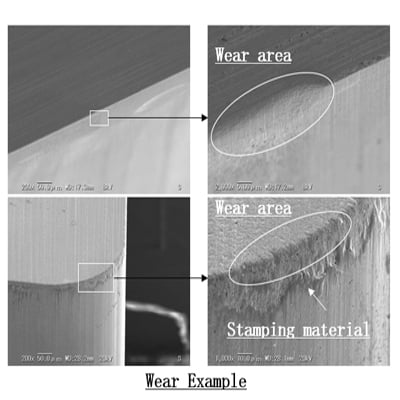
Karbür kullanım süreci ile ilgili bazı sorularımız olacak, sizlere cevap sağlamak için yıllardır sektördeki vakaları inceliyoruz.
1. Çimentolu Karbürün işlenmesinden sonra küçük çatlaklar ortaya çıkar
Çimentolu Karbürün tel kesme veya kıvılcım makinesi deşarj işlemesi sırasında mikro çatlak oluşma olasılığı vardır. Mikro parçacık veya ultra mikro parçacık alaşımlarında küçük çatlakların oluşma olasılığı daha yüksektir. İşlenmiş iş parçasında veya bitmiş iş parçasında lokal çatlaklar oluşmasına neden olabilir.
Neden:
Tel EDM'de karbürün yüksek sıcaklıkta çözünmesi sonucu oluşan hızlı söndürme ve soğutma sonucu oluşan yoğuşma.
Çözüm ve Öneri:
WEDM sırasında akım yükünü azaltın (tel kesme süresini artırın).
Mikro çatlakların giderilmesi: Finisaj işlemi için zımpara makinesi kullanılması önerilir.
Metamorfik tabakalar ve mikro çatlaklar içeren malzemelerin işlenmesi sırasında, öğütme işlemi sırasında oluşan yük nedeniyle kırılma ve dökülmeler meydana gelebilir.
2.Tungsten karbür aşınmış
Elektriksel deşarj işlemede su kullanımı nedeniyle, semente karbürün yüzeyinde galvanik korozyon meydana gelebilir. Kobalt içeriği daha yüksek olduğunda, galvanik korozyon meydana gelme olasılığı daha yüksektir. Ayrıca, depolama sırasında korozyon meydana gelebilir.
Neden:
Su kullanılarak yapılan elektriksel deşarj işlemede, akım teması galvanik korozyona neden olabilir, aynı şekilde neme maruz kalma da galvanik korozyona neden olabilir.
Çözüm ve Öneri:
İşleme suyunun direncini artırın.
Korozyona dayanıklı karbür kullanın (Yatech Malzemeler YA veya YF serisi karbür).
Kuru ortamda saklayınız.
Paslanmaya dayanıklı yağ kullanın.
*Yağlı EDM işleminde korozyon meydana gelmez.
3. Çimentolu Karbür Tel EDM'deki Çatlaklar
Tel kesmeli elektriksel deşarj işleme sırasında karbürde çatlaklar meydana gelebilir.
Neden:
Tel EDM çatlamasına, EDM işlemi sırasında oluşan yüksek ısı ve iç gerilmeler de dahil olmak üzere çeşitli faktörler neden olur.
Isıl şok, küçük çatlaklar, metamorfik tabakalar, galvanik korozyon vb.
Çözümler ve Öneriler
Tel EDM (temel eleman) öncesi karbürün üst ve alt yüzeylerini keskinleştirin.
Karbürün dış kısmından iç kısmına doğru kesin, ortasında delik açmayın.
Daha ince malzeme kullanın
4.Tungsten karbür dökülmesi
Tungsten karbür yüksek mukavemete sahiptir ve aşınmaya karşı dirençlidir. Ancak, işleme yükleri yüksek olduğunda, tungsten karbürde pullanma meydana gelebilir ve bu da kenarın körelmesine neden olabilir.
Sebep:
Taşlama işleminde çok fazla işleme yükü.
Tungsten karbürün (WC) kaba parçacıkları.
Çözüm ve öneri:
Öğütme yükünü azaltın.
Mikro partikül alaşımlarını ve yüksek kobalt içerikli alaşımları seçin.
5.Karbürlü kırık kenarlar ve köşeler
Karbür sert ve kırılgan olduğundan bazen kırılmalar meydana gelebilir.
Sebep:
Elleçleme ve işleme sırasındaki darbe
Parçanın boyutsal doğruluğu çok düşüktür ve çok yönlü kuvvetler mevcuttur.
Çözümler ve Öneriler
İşleme esnasında parçaya vurmayın ve aşırı darbe kuvveti uygulamayın.
Ürünün boyutsal doğruluğunu artırın.
Bileme.
6.Semente Karbür Aşınması
Sinterlenmiş Karbür aşınması uygulamadan uygulamaya değişir. Karbürün yoğunluğu arttıkça aşınma azalır. Ancak, yüksek yoğunluklu alaşımlar parçalanmaya eğilimlidir. Ayrıca, aşınma damgalanan malzemenin türüne bağlı olarak değişir.
Neden
Düşük yoğunluklu alaşımlı malzeme veya damgalama malzemesinin iş parçasına yapışması.
Çözümler ve Öneriler
İş parçası malzemesinin yoğunluğunu artırın.
Yapışma önleyici malzemeli iş parçası kullanın. Öneri: Düşük kobalt içeriğine sahip bir alaşım olan YA10.