Carbide drawing dies, Wire Dies
Standard Carbide drawing dies and custom drawing dies.
various shapes, including round, square, and complex designs.
Sintered carbide nibs are offered for wire diameters ranging from 0.10 mm to 15.00 mm, with a carbide grade specifically developed for drawing dies.
This grade provides exceptional wear resistance and improved coating performance.
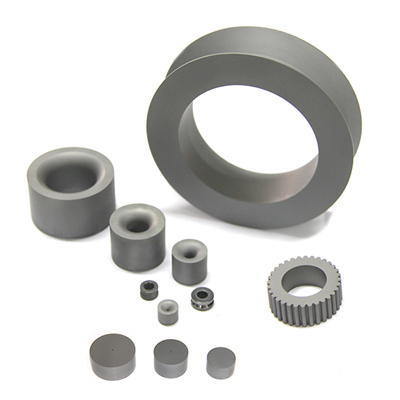
Carbide Drawing Dies Grades
Grades | Physical Properties | Areas of Application | Major application and characteristics | ||||
Hardness | Density | TRS | Corrosion | Erosion | Toughness | ||
HRA | g/cm3 | N/mm2 | C | E | T | ||
YF50H | 88.2-89.2 | 13.95-14.15 | ≥3000 | ▲ | ● | ■ | It is suitable to produce sleeves and other wear parts used in oil & gas and chemistry industry due to high impact-resistance and wear resistance. |
YK35 | 88.5-89.5 | 14.30-14.50 | ≥2800 | ▲ | ● | ■ | It is suitable to produce sleeves bushings and nozzles dur to high hardness and good wear-resistance, |
YV25 | 88.7-89.7 | 14.20-14.50 | ≥3200 | ▲ | ■ | ● | It is suitable to produce high pressure nozzle, threaded nozzles, bushings and valves used in oil & gas and chemistry industry due to high impact-resistance and wear resistance, |
YK40A | 90.5-91.5 | 14.50-14.70 | ≥2800 | ● | ■ | ▲ | It is suitable to produce sleeves and nozzles used in oil & gas industry due to high hardness and good wear-resistance, |
YK30H | 89.5-90.5 | 14.7-14.8 | ≥2800 | ▲ | ● | ■ | It is suitable to produce sleeves and bushings due to good wear resistance and toughness. |
YU10 | 92.5-93.5 | 14.8-15.00 | ≥2700 | ▲ | ● | ■ | It is suitable to produce sleeves and bushings due to high hardness and good wear-resistance. |
YK05A | 92.0-93.0 | 14.80-15.00 | ≥2450 | ▲ | ● | ■ | It is suitable to produce wear parts used for oil-immersed pump, valve point and valve seat due to excellent wear resistance and high toughness, |
YA25N | 88.3-89.3 | 13.85-14.05 | ≥2700 | ● | ■ | ▲ | It is suitable to produce wear parts for stabilizer and other parts used in oil & gas industry due to good wear-resistance and corrosion resistance, |
YD10N | 87.5-89.0 | 14.40-14.60 | ≥2400 | ● | ■ | ■ | It is suitable to produce valve balls and seats as well as other vale products used in oil & gas industry due to excellent corrosion & erosion resistance, |
YD06N | 89.0-90.5 | 14.80-15.00 | ≥1900 | ● | ■ | ▲ | It is suitable to produce valve balls and seats as well as other vale products used in oil & gas industry due to excellent corrosion & erosion resistance, |
YF06N | 90.2-91.2 | 14.80-15.00 | ≥1760 | ● | ■ | ▲ | It is suitable to produce sleeves and bushings used in oil & gas industry due to excellent corrosion & erosion resistance, |
● Recommended application area ■ Secondary application area ▲ Alternative application area |
CVD Drawing Dies
The nano-diamond composite coating drawing die is created using cemented carbide (WC-Co) as a base and employing chemical vapor deposition (CVD) to apply micron-level and nano-level diamond composite coating on the mold’s inner hole surface. Subsequent to precisely grinding and polishing the coating, a brand-new mold is obtained. The micro-nano composite coating on the surface of the inner hole possesses not only the strong adhesion and good wear resistance of the micro-diamond coating, but also the advantages of high surface finish, low friction coefficient, and facile grinding and polishing of the nano-diamond coating.
- Targeted pretreatment process: the coating is tightly bonded to the substrate.
- Bottom micron diamond coating: excellent wear resistance.
- Surface nanoscale diamond coating: excellent surface finish and low coefficient of friction.
- Computer simulation to optimize the pass design: make the wire stress uniform.
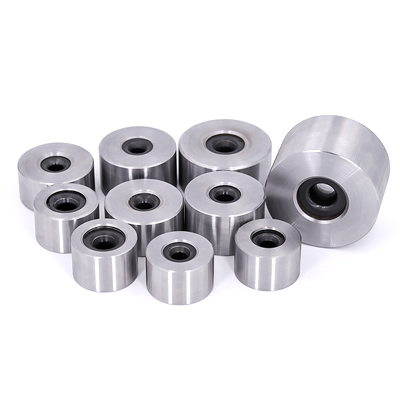