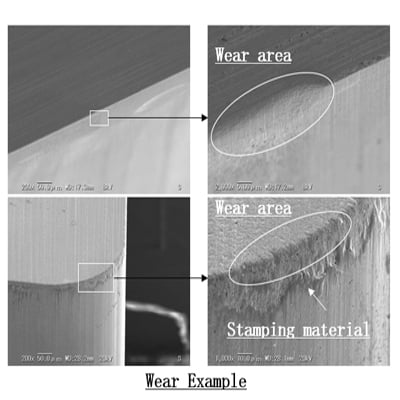
Proces stosowania węglików spiekanych rodzi pewne pytania, na które odpowiedzi udzieliliśmy na podstawie wieloletnich badań branżowych.
1. Po obróbce węglika spiekanego pojawiają się drobne pęknięcia
Istnieje możliwość mikropęknięć podczas cięcia drutem lub obróbki wyładowczej węglika spiekanego. Drobne pęknięcia są bardziej prawdopodobne w stopach mikrocząsteczkowych lub ultramikrocząsteczkowych. Może to skutkować lokalnymi pęknięciami obrabianego przedmiotu obrabianego lub gotowego przedmiotu obrabianego.
Przyczyna:
Kondensacja powstająca w wyniku szybkiego hartowania i chłodzenia po rozpuszczeniu węglika w wysokiej temperaturze podczas obróbki elektroerozyjnej drutem.
Rozwiązanie i sugestia:
Zmniejsz obciążenie prądowe podczas obróbki WEDM (zwiększ czas cięcia drutu).
Usuwanie mikropęknięć: Do wykańczania zaleca się użycie szlifierki.
Podczas obróbki materiałów z warstwami metamorficznymi i mikropęknięciami może dojść do odpryskiwania i łuszczenia się materiału na skutek obciążeń występujących w procesie szlifowania.
2. Węglik wolframu skorodowany
Z powodu stosowania wody w obróbce elektroerozyjnej, korozja galwaniczna może wystąpić na powierzchni węglika spiekanego. Gdy zawartość kobaltu jest wyższa, korozja galwaniczna jest bardziej prawdopodobna. Ponadto korozja może wystąpić podczas przechowywania.
Przyczyna:
Podczas obróbki elektroerozyjnej z wykorzystaniem wody, kontakt z prądem może powodować korozję galwaniczną, podobnie jak narażenie na wilgoć.
Rozwiązanie i rekomendacja:
Zwiększenie rezystywności wody obrabianej mechanicznie.
Użyj węglika odpornego na korozję (Yatech Materiały (węglik spiekany serii YA lub YF).
Przechowywać w suchym miejscu.
Stosuj olej odporny na rdzę.
*Podczas obróbki elektroerozyjnej z użyciem oleju nie będzie występowała korozja.
3. Pęknięcia w elektroerozyjnej obróbce drutem z węglika spiekanego
Podczas obróbki elektroerozyjnej drutem mogą wystąpić pęknięcia węglika spiekanego.
Przyczyna:
Na pękanie drutów podczas obróbki elektroerozyjnej ma wpływ wiele czynników, w tym wysoka temperatura i naprężenia wewnętrzne występujące podczas procesu obróbki elektroerozyjnej.
Wstrząsy termiczne, drobne pęknięcia, warstwy metamorficzne, korozja galwaniczna, itp.
Rozwiązania i zalecenia
Przed przystąpieniem do obróbki elektroerozyjnej drutem (element podstawowy) należy naostrzyć górną i dolną powierzchnię węglika spiekanego.
Tnij węglik od zewnątrz do wewnątrz, nie wycinaj otworów w środku.
Użyj cieńszego materiału
4. Łuszczenie węglika wolframu
Węglik wolframu ma wysoką wytrzymałość i jest odporny na zużycie. Jednak gdy obciążenia obróbcze są wysokie, może wystąpić łuszczenie się węglika wolframu, powodując stępienie krawędzi.
Powód:
Zbyt duże obciążenie podczas obróbki w procesie szlifowania.
Grube cząstki węglika wolframu (WC).
Rozwiązanie i sugestia:
Zmniejsz obciążenie szlifierskie.
Wybieraj stopy mikrocząsteczkowe i stopy o wysokiej zawartości kobaltu.
5. Krawędzie i narożniki z wiórami węglikowymi
Ponieważ węglik spiekany jest twardy i kruchy, czasami może dojść do jego wykruszenia.
Powód:
Uderzenia podczas obsługi i przetwarzania
Dokładność wymiarowa części jest zbyt niska i występują siły wielokierunkowe.
Rozwiązania i zalecenia
Nie uderzaj w część i nie stosuj nadmiernej siły uderzeniowej podczas obróbki.
Poprawa dokładności wymiarowej produktu.
Szlifowanie.
6.Zużycie węglika spiekanego
Zużycie węglika spiekanego zmienia się w zależności od zastosowania. Wraz ze wzrostem gęstości węglika zużycie maleje. Jednak stopy o wysokiej gęstości są podatne na łuszczenie. Ponadto zużycie zmienia się w zależności od rodzaju tłoczonego materiału.
Przyczyna
Materiał stopowy o małej gęstości lub przyklejenie materiału tłoczącego do przedmiotu obrabianego.
Rozwiązania i zalecenia
Zwiększenie gęstości materiału obrabianego.
Użyj przedmiotu obrabianego z materiałem antyadhezyjnym. Zalecenie: YA10, stop o niskiej zawartości kobaltu.