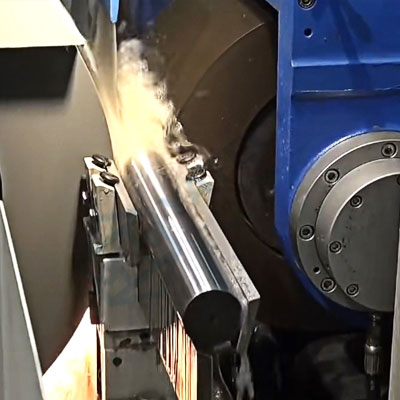
超硬棒の研削入門
セメンテッド 超硬棒 ~の製造に広く使用されています 切削工具エンドミル、ドリル、リーマーなど。硬度が高く、強度が高く、耐摩耗性、耐高温性、耐食性などの優れた特性を備えています。特に硬度と耐摩耗性が高く、1000℃でも高い硬度を維持します。
ただし、研削は固着します 超硬棒 それは簡単な仕事ではありません。砥石の品質と性能に影響を与える可能性のある研削焼けや亀裂を避けるために、砥石車と冷却方法を慎重に選択する必要があります。 ロッド。今回は超硬合金の特徴と砥石の選定、超硬合金を研削する際の冷却方法について紹介します。 超硬棒.
超硬合金の特徴
超硬合金は、硬質炭化物粒子 (炭化タングステン、炭化チタン、炭化タンタルなど) と金属結合剤 (コバルト、ニッケル、鉄など) で構成される複合材料です。炭化物と結合剤の割合と組成は、超硬合金の用途と望ましい特性に応じて変わります。
超硬合金の主な利点は次のとおりです。
– 高い硬度と耐摩耗性: 超硬合金の硬度範囲は 75 ~ 95 HRA (ロックウェル A スケール) で、ほとんどの金属や合金よりもはるかに高くなります。刃先を失うことなく、高速切断、研磨材、高温に耐えることができます。また、摩擦係数が低く、弾性率が高いため、工具の摩耗や変形が軽減されます。
– 優れた強度と靭性:超硬合金は高い圧縮強度と適度な引張強度を備えているため、切断時の曲げ、破損、欠けに耐えることができます。また、耐衝撃性と衝撃吸収性に優れているため、脆性破壊を防止し、工具寿命が向上します。
– 優れた化学的安定性と耐食性: 超硬合金は、ほとんどの酸、アルカリ、有機溶剤に対して不活性です。酸化、錆び、孔食、電気腐食に耐性があります。また、硬度や強度を失うことなく高温に耐えることができます。
ただし、超硬合金には次のような欠点もあります。
– 高コスト: 超硬合金は、複雑な製造プロセスと希少な原材料のため、ほとんどの金属や合金よりも高価です。また、機械加工や研削のための特別な設備と技術も必要です。
– 低い熱伝導率:超硬合金は金属に比べて熱伝導率が低いため、切断または研削中に熱が蓄積します。これにより、工具やワークピースに熱膨張、熱応力、または熱衝撃が生じる可能性があります。
– 低延性: 超硬合金は金属に比べて延性が低いため、破損せずに塑性変形する能力が限られています。過度な力や衝撃が加わると、工具やワークに亀裂や破損が生じる可能性があります。
超硬棒研削用砥石の選定
研削は、高速回転する研磨工具 (砥石車など) を使用してワークピースから材料を除去するプロセスです。研削加工により、ワークの高精度、表面仕上げ、寸法公差を実現できます。ただし、研削では熱、摩擦、振動も発生し、ワークピースや工具に損傷を与える可能性があります。
研削セメンテッド 超硬棒 硬度が高く熱伝導率が低いため、特に困難です。したがって、
良好な研削結果を得るには、研削砥石の選択が非常に重要です。
砥石は砥粒(ダイヤモンドや立方晶窒化ホウ素など)、結合材(金属や樹脂など)、気孔(砥粒間の隙間)で構成されています。砥粒は、ワークピースから材料を切断または除去する役割を果たします。結合材は粒子を結合し、ホイールの強度と形状を決定します。この細孔により、クーラントがホイールを通って流れ、熱と切り粉が運び去られます。
超硬砥石を選択する際に考慮すべき主な要素 超硬棒 は:
– 研磨材の種類: 研磨材のタイプは、被削材の硬度と靭性に適合する必要があります。セメンテッド用 超硬棒,
ダイヤモンドは最高の硬度 (モース スケールで 10) を持ち、あらゆる材料を切断できるため、最も一般的に使用される研磨剤です。立方晶窒化ホウ素 (CBN) は、ダイヤモンドよりも硬度がわずかに低い (モース スケールで 9) ものの、熱安定性が高いもう 1 つのオプションです。 CBN は、コバルト含有量が高い超硬合金、またはチタンまたはタンタル添加剤を含む超硬合金の研削に使用できます。
– 結合タイプ: 結合タイプは研削条件と要件に一致する必要があります。セメンテッド用 超硬棒、金属ボンドと樹脂ボンドが最も一般的に使用されます。メタルボンドは強度と剛性が高く、砥粒をしっかりと保持しホイールの形状を維持します。メタルボンドは荒研削、重研削、高速研削に適しています。レジンボンドは強度と剛性が低いため、砥粒が自己研磨して簡単に剥がれてしまいます。レジンボンドは微研削、精密研削、低速研削に適しています。
– 粒子サイズ: 粒子サイズは、研削の切断効率と表面仕上げを決定します。粒子サイズは、粒子を通過させることができるふるいの直線インチあたりの開口部の数を示すメッシュ番号によって測定されます。メッシュ番号が大きいほど、粒度は小さくなります。セメンテッド用 超硬棒、一般的な粒度は 80 ~ 400 メッシュの範囲です。粒度が小さいほど表面は滑らかに仕上がりますが、切削効率は低くなります。粒子サイズが大きいほど、表面仕上げは粗くなりますが、切削効率は高くなります。
– ホイール形状: ホイール形状は、ホイールとワークピース間の接触面積と圧力を決定します。ホイールの形状は、文字と数字からなる標準コードによって分類されます。文字は、A (ストレート)、B (円筒)、D (カップ) などのホイールの基本形状を示します。数字は、1 (平坦)、2 (凹面) など、ホイールの特定のプロファイルを示します。 、3(凸)などセメンテッド用 超硬棒、一般的なホイールの形状は、A1 (ストレート フラット)、D1 (カップ フラット)、または D6 (カップ フレア) です。
D6仕様のエンドミルを例に、一般的な砥石の選定を表1に示します。
研削工程 | 砥石 |
---|---|
刃研削 | D6A2 150/200メッシュメタルボンドダイヤモンド |
ガッシュ研削 | D1A1 150/200メッシュメタルボンドダイヤモンド |
すきま研削 | D6A2 150/200メッシュメタルボンドダイヤモンド |
端面研削 | D6A2 150/200メッシュ レジンボンドダイヤモンド |
超硬棒を研削するための冷却方法
冷却はワークピースや工具への熱による損傷を防止または軽減できるため、研削には不可欠な部分です。冷却により、ワークの切削効率、表面仕上げ、寸法精度も向上します。
冷却は、熱と切り粉を除去するために研削ゾーン中またはその周囲を流れる液体または気体である冷媒を使用することによって実現できます。クーラントは、ワークピースや工具を潤滑し、腐食や酸化から保護することもできます。
超硬ロッドを研削するためのクーラントを選択する際に考慮すべき主な要素は次のとおりです。
– クーラントの種類: クーラントの種類はワークの材質と研削条件に適合する必要があります。セメンテッド用 超硬棒,
水ベースのクーラントは、冷却性能が高く、粘度が低く、コストが低く、環境への影響が少ないため、油ベースのクーラントよりも好まれます。水ベースの冷却剤には、純水、または合成油、エマルジョン、溶液などの添加剤を混合した水が使用できます。添加剤は、冷却剤の潤滑性、安定性、耐腐食性、防錆性、または消泡性を向上させることができます。
– 冷却液の温度: 冷却液の温度は、熱を効果的に除去できる程度に低くする必要がありますが、ワークピースや工具に熱衝撃や結露を引き起こすほど低すぎてはなりません。超硬ロッドの場合、 超硬棒,
最適な冷却剤温度は 15°C ~ 25°C の範囲です。
– クーラント圧力: クーラント圧力は、研削ゾーンに浸透して切りくずを洗い流すのに十分な高さである必要がありますが、ワークピースや工具に飛沫や浸食を引き起こすほど高すぎてはなりません。超硬ロッドの場合、 超硬棒,
最適なクーラント圧力の範囲は 0.5 MPa ~ 2 MPa です。
– 冷却剤の流量: 冷却剤の流量は、研削ゾーン全体をカバーし、十分な冷却を提供するのに十分である必要がありますが、冷却剤を無駄にしたり環境問題を引き起こしたりするほど過剰ではありません。超硬ロッドの場合、 超硬棒,
最適な冷却液流量の範囲は 5 L/min ~ 20 L/min です。
– クーラント注入位置: クーラント注入位置は研削ゾーンの近くにあり、研削ゾーンの方向と一致している必要があります。
ホイールの回転と送りの動き。これにより、クーラントが迅速かつ効果的に切削領域に到達し、切削領域を妨げないようにすることができます。
切りくずの排出や気泡の発生を防ぎます。
工具チップの溝を研削する場合、クーラントの注入位置は図 1 に示すようにすることをお勧めします。
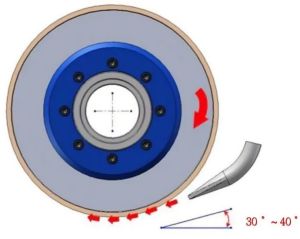
結論
研削セメンテッド 超硬棒 挑戦的ですが、高品質を生み出すことができるやりがいのあるプロセスです 切削工具 優れた性能と耐久性を備えています。ただし細心の注意が必要です