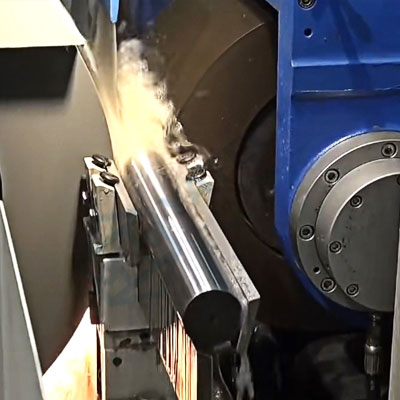
مقدمه ای بر سنگ زنی میله های کاربید سیمانی
سیمانی شده میله های کاربید به طور گسترده در ساخت استفاده می شود ابزار برشمانند آسیاب های انتهایی، مته ها و ریمرها. آنها دارای سختی بالا، استحکام خوب و یک سری خواص عالی مانند مقاومت در برابر سایش، مقاومت در برابر دمای بالا و مقاومت در برابر خوردگی هستند. به خصوص سختی و مقاومت بالای آنها که در دمای 1000 درجه سانتیگراد همچنان سختی بالایی دارند.
با این حال، سنگ زنی سیمان میله های کاربید کار آسانی نیست این نیاز به انتخاب دقیق چرخ های سنگ زنی و روش های خنک کننده دارد تا از سوختگی ها و ترک هایی که می تواند بر کیفیت و عملکرد دستگاه تأثیر بگذارد جلوگیری شود. میله ها. در این مقاله به معرفی ویژگی های کاربید سیمانی، انتخاب چرخ سنگ زنی و روش های خنک کاری آسیاب سیمان می پردازیم. میله های کاربید.
ویژگی های کاربید سیمانی
کاربید سیمانی یک ماده کامپوزیتی است که از ذرات سخت کاربید (مانند کاربید تنگستن، کاربید تیتانیوم یا کاربید تانتالیوم) و یک اتصال دهنده فلزی (مانند کبالت، نیکل یا آهن) تشکیل شده است. نسبت و ترکیب کاربید و بایندر بسته به کاربرد و خواص مورد نظر کاربید سیمانی می تواند متفاوت باشد.
مزایای اصلی کاربید سیمانی عبارتند از:
- سختی و مقاومت در برابر سایش بالا: کاربید سیمانی دارای محدوده سختی 75-95 HRA (مقیاس Rockwell A) است که بسیار بالاتر از اکثر فلزات و آلیاژها است. می تواند سرعت های برش بالا، مواد ساینده و دماهای بالا را بدون از دست دادن لبه خود تحمل کند. همچنین دارای ضریب اصطکاک کم و مدول الاستیسیته بالایی است که باعث کاهش سایش و تغییر شکل ابزار می شود.
- استحکام و چقرمگی خوب: کاربید سیمانی دارای استحکام فشاری بالا و استحکام کششی متوسطی است که آن را قادر میسازد در برابر خمش، شکستن و خرد شدن در حین برش مقاومت کند. همچنین دارای مقاومت خوبی در برابر ضربه و جذب ضربه است که از شکستگی شکننده جلوگیری می کند و عمر ابزار را بهبود می بخشد.
- پایداری شیمیایی خوب و مقاومت در برابر خوردگی: کاربید سیمانی نسبت به اکثر اسیدها، قلیایی ها و حلال های آلی بی اثر است. می تواند در برابر اکسیداسیون، زنگ زدگی، سوراخ شدن و خوردگی گالوانیکی مقاومت کند. همچنین می تواند بدون از دست دادن سختی یا استحکام در برابر دمای بالا مقاومت کند.
با این حال، کاربید سیمانی دارای معایبی نیز می باشد، از جمله:
- هزینه بالا: کاربید سیمانی به دلیل فرآیند پیچیده ساخت و مواد اولیه کمیاب، گرانتر از اکثر فلزات و آلیاژها است. همچنین به تجهیزات و تکنیک های خاصی برای ماشین کاری و سنگ زنی نیاز دارد.
– هدایت حرارتی کم: کاربید سیمانی در مقایسه با فلزات رسانایی حرارتی پایینی دارد، به این معنی که در هنگام برش یا سنگ زنی گرما را جمع می کند. این می تواند باعث انبساط حرارتی، استرس حرارتی یا شوک حرارتی در ابزار یا قطعه کار شود.
– شکل پذیری کم: کاربید سیمانی در مقایسه با فلزات انعطاف پذیری کمی دارد، به این معنی که توانایی محدودی برای تغییر شکل پلاستیکی بدون شکستگی دارد. این می تواند در صورت قرار گرفتن در معرض نیرو یا ضربه بیش از حد باعث ایجاد ترک یا شکستگی در ابزار یا قطعه کار شود.
انتخاب چرخ سنگ زنی برای سنگ زنی میله های کاربید سیمانی
سنگ زنی فرآیندی است برای حذف مواد از قطعه کار با استفاده از ابزار ساینده (مانند چرخ سنگ زنی) که با سرعت بالا می چرخد. سنگ زنی می تواند به دقت بالا، پرداخت سطح و تحمل ابعادی برای قطعه کار دست یابد. با این حال، سنگ زنی همچنین گرما، اصطکاک و لرزش ایجاد می کند که می تواند به قطعه کار یا ابزار آسیب برساند.
سنگ زنی سیمانی میله های کاربید به خصوص به دلیل سختی بالا و هدایت حرارتی کم آنها چالش برانگیز است. بنابراین،
انتخاب چرخ سنگ زنی برای دستیابی به نتایج خوب سنگ زنی بسیار حیاتی است.
چرخ سنگ زنی از دانه های ساینده (مانند الماس یا نیترید بور مکعبی)، مواد پیوندی (مانند فلز یا رزین) و منافذ (فضاهای بین دانه ها) تشکیل شده است. دانه های ساینده مسئول برش یا حذف مواد از قطعه کار هستند. مواد چسبنده دانه ها را در کنار هم نگه می دارد و استحکام و شکل چرخ را تعیین می کند. منافذ به مایع خنک کننده اجازه می دهد تا از چرخ عبور کند و گرما و تراشه ها را از خود دور کند.
فاکتورهای اصلی که باید هنگام انتخاب چرخ سنگ زنی برای سیمان در نظر گرفت میله های کاربید عبارتند از:
– نوع ساینده: نوع ساینده باید با سختی و چقرمگی مواد قطعه کار مطابقت داشته باشد. برای سیمان میله های کاربید,
الماس متداول ترین ساینده مورد استفاده است زیرا دارای بالاترین سختی (10 در مقیاس Mohs) است و می تواند هر ماده ای را برش دهد. نیترید بور مکعبی (CBN) گزینه دیگری است که سختی کمی کمتر (9 در مقیاس Mohs) اما پایداری حرارتی بالاتر از الماس دارد. CBN را می توان برای آسیاب کاربیدهای سیمانی با محتوای کبالت بالا یا با افزودنی های تیتانیوم یا تانتالیوم استفاده کرد.
– نوع پیوند: نوع باند باید با شرایط و الزامات سنگ زنی مطابقت داشته باشد. برای سیمان میله های کاربید، پیوندهای فلزی و رزینی بیشترین استفاده را دارند. اتصالات فلزی استحکام و استحکام بالایی دارند که می تواند دانه های ساینده را محکم نگه دارد و شکل چرخ را حفظ کند. پیوندهای فلزی برای سنگ زنی خشن، سنگ زنی سنگین یا سنگ زنی با سرعت بالا مناسب هستند. باندهای رزین دارای استحکام و سفتی پایینی هستند که می تواند به دانه های ساینده اجازه دهد تا خود تیز شوند و به راحتی آزاد شوند. پیوندهای رزین برای سنگ زنی ریز، سنگ زنی دقیق یا آسیاب با سرعت پایین مناسب هستند.
– اندازه دانه: اندازه دانه، کارایی برش و پرداخت سطحی آسیاب را تعیین می کند. اندازه دانه با عدد مش اندازه گیری می شود که نشان دهنده تعداد دهانه ها در هر اینچ خطی در غربال است که می تواند دانه ها را عبور دهد. هرچه عدد مش بیشتر باشد، اندازه دانه کوچکتر است. برای سیمان میله های کاربیداندازه دانه معمولی بین 80 تا 400 مش است. اندازه دانه کوچکتر می تواند سطح صاف تری را ایجاد کند اما راندمان برش کمتری دارد. اندازه دانه بزرگتر می تواند سطحی زبرتر را ایجاد کند اما راندمان برش بالاتری دارد.
– شکل چرخ: شکل چرخ سطح تماس و فشار بین چرخ و قطعه کار را تعیین می کند. شکل چرخ توسط یک کد استاندارد که از یک حرف و یک عدد تشکیل شده است طبقه بندی می شود. این حرف شکل اصلی چرخ را نشان میدهد، مانند A (مستقیم)، B (اسوانهای)، D (کاپ) و غیره. ، 3 (محدب) و غیره برای سیمان میله های کاربیدشکل چرخ های معمولی A1 (مستقیم صاف)، D1 (فنجان مسطح)، یا D6 (فنجان باز شده).
با در نظر گرفتن آسیاب انتهایی مشخصات D6 به عنوان مثال، انتخاب چرخ سنگزنی رایج در جدول 1 نشان داده شده است.
فرآیند سنگ زنی | چرخ سنگ زنی |
---|---|
سنگ زنی فلوت | الماس باند فلزی 150/200 مش D6A2 |
سنگ زنی گاز | الماس باند فلزی مش 150/200 D1A1 |
ترخیص سنگ زنی | الماس باند فلزی 150/200 مش D6A2 |
پایان چهره زنی | الماس باند رزین مش 150/200 D6A2 |
روش های خنک کننده برای آسیاب میله های کاربید سیمانی
خنک کردن بخش ضروری سنگ زنی است زیرا می تواند از آسیب حرارتی به قطعه کار یا ابزار جلوگیری یا کاهش دهد. خنک کننده همچنین می تواند کارایی برش، پرداخت سطح و دقت ابعاد قطعه کار را بهبود بخشد.
خنکسازی را میتوان با استفاده از یک خنککننده، که مایع یا گازی است که از طریق یا اطراف منطقه آسیاب جریان مییابد تا گرما و برادهها را از بین ببرد، حاصل شود. مایع خنک کننده همچنین می تواند قطعه کار و ابزار را در برابر خوردگی یا اکسیداسیون روغن کاری کرده و از آن محافظت کند.
فاکتورهای اصلی که هنگام انتخاب یک خنک کننده برای آسیاب میله های کاربید سیمانی باید در نظر گرفته شود عبارتند از:
- نوع خنک کننده: نوع خنک کننده باید با مواد قطعه کار و شرایط آسیاب مطابقت داشته باشد. برای سیمان میله های کاربید,
خنک کننده های مبتنی بر آب به خنک کننده های مبتنی بر روغن ترجیح داده می شوند زیرا عملکرد خنک کنندگی بهتر، ویسکوزیته کمتر، هزینه کمتر و اثرات زیست محیطی کمتری دارند. خنک کننده های مبتنی بر آب می توانند آب خالص یا آب مخلوط با مواد افزودنی مانند روغن های مصنوعی، امولسیون ها یا محلول ها باشند. افزودنی ها می توانند خاصیت روانکاری، پایداری، ضد خوردگی، ضد زنگ یا ضد کف بودن مایع خنک کننده را افزایش دهند.
– دمای مایع خنککننده: دمای مایع خنککننده باید به اندازهای پایین باشد که گرما را به طور موثر حذف کند، اما نه آنقدر پایین باشد که باعث ایجاد شوک حرارتی یا تراکم بر روی قطعه کار یا ابزار شود. برای سیمان میله های کاربید,
دمای مطلوب مایع خنک کننده از 15 درجه سانتیگراد تا 25 درجه سانتیگراد است.
– فشار مایع خنککننده: فشار مایع خنککننده باید به اندازهای زیاد باشد که به منطقه آسیاب نفوذ کند و تراشهها را از بین ببرد، اما نه آنقدر زیاد که باعث پاشش یا فرسایش روی قطعه کار یا ابزار شود. برای سیمان میله های کاربید,
فشار بهینه خنک کننده از 0.5 مگاپاسکال تا 2 مگاپاسکال است.
- سرعت جریان مایع خنک کننده: سرعت جریان مایع خنک کننده باید به اندازه ای باشد که کل منطقه آسیاب را پوشش دهد و خنک کننده کافی را فراهم کند اما نه بیش از حد برای هدر رفتن مایع خنک کننده یا ایجاد مشکلات زیست محیطی. برای سیمان میله های کاربید,
دبی بهینه مایع خنک کننده از 5 لیتر در دقیقه تا 20 لیتر در دقیقه متغیر است.
– موقعیت تزریق مایع خنککننده: موقعیت تزریق مایع خنککننده باید نزدیک به ناحیه آسیاب باشد و با جهت
چرخش چرخ و حرکت تغذیه این می تواند تضمین کند که مایع خنک کننده به سرعت و به طور موثر به منطقه برش می رسد و تداخلی با آن ایجاد نمی کند
تخلیه تراشه یا ایجاد حباب های هوا.
پیشنهاد می شود که هنگام سنگ زنی شیار تراشه ابزار، موقعیت تزریق مایع خنک کننده در شکل 1 نشان داده شده است.
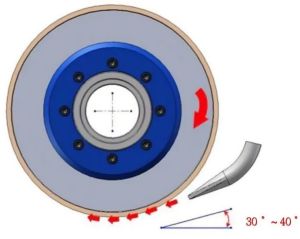
نتیجه
سنگ زنی سیمانی میله های کاربید فرآیندی چالش برانگیز اما پر ارزش است که می تواند کیفیت بالایی تولید کند ابزار برش با عملکرد و دوام عالی با این حال، نیاز به توجه دقیق دارد