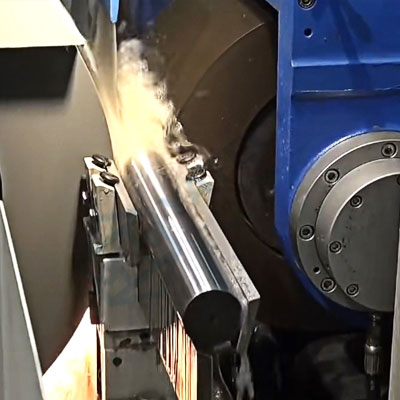
Introduction au meulage des tiges de carbure cémenté
Cimenté tiges de carbure sont largement utilisés dans la fabrication de outils de coupe, tels que les fraises en bout, les forets et les alésoirs. Ils ont une dureté élevée, une bonne résistance et une série d'excellentes propriétés telles que la résistance à l'usure, la résistance aux températures élevées et la résistance à la corrosion. Surtout leur dureté et leur résistance à l'usure élevées, qui conservent une dureté élevée même à 1000°C.
Cependant, le broyage cimenté tiges de carbure n'est pas une tâche facile. Cela nécessite une sélection minutieuse des meules et des méthodes de refroidissement pour éviter les brûlures et les fissures qui peuvent affecter la qualité et les performances du tiges. Dans cet article, nous présenterons les caractéristiques du carbure cémenté, la sélection des meules et les méthodes de refroidissement pour le meulage du carbure cémenté. tiges de carbure.
Caractéristiques du carbure cémenté
Le carbure cémenté est un matériau composite composé de particules de carbure dur (comme le carbure de tungstène, le carbure de titane ou le carbure de tantale) et d'un liant métallique (comme le cobalt, le nickel ou le fer). La proportion et la composition du carbure et du liant peuvent varier en fonction de l'application et des propriétés souhaitées du carbure cémenté.
Les principaux avantages du carbure cémenté sont :
– Dureté et résistance à l'usure élevées : le carbure cémenté a une plage de dureté de 75 à 95 HRA (échelle Rockwell A), ce qui est beaucoup plus élevé que la plupart des métaux et alliages. Il peut résister à des vitesses de coupe élevées, à des matériaux abrasifs et à des températures élevées sans perdre son tranchant. Il présente également un faible coefficient de frottement et un module d'élasticité élevé, qui réduisent l'usure et la déformation de l'outil.
– Bonne résistance et ténacité : Le carbure cémenté a une résistance élevée à la compression et une résistance à la traction modérée, ce qui lui permet de résister à la flexion, à la rupture et à l’écaillage lors de la coupe. Il présente également une bonne résistance aux chocs et une bonne absorption des chocs, ce qui évite les fractures fragiles et améliore la durée de vie de l'outil.
– Bonne stabilité chimique et résistance à la corrosion : le carbure cémenté est inerte vis-à-vis de la plupart des acides, alcalis et solvants organiques. Il peut résister à l’oxydation, à la rouille, aux piqûres et à la corrosion galvanique. Il peut également résister à des températures élevées sans perdre sa dureté ou sa résistance.
Cependant, le carbure cémenté présente également certains inconvénients, tels que :
– Coût élevé : Le carbure cémenté est plus cher que la plupart des métaux et alliages en raison de son processus de fabrication complexe et de la rareté de ses matières premières. Cela nécessite également des équipements et des techniques spéciaux pour l’usinage et le meulage.
– Faible conductivité thermique : Le carbure cémenté a une faible conductivité thermique par rapport aux métaux, ce qui signifie qu'il accumule de la chaleur lors de la coupe ou du meulage. Cela peut provoquer une dilatation thermique, une contrainte thermique ou un choc thermique dans l'outil ou la pièce.
– Faible ductilité : Le carbure cémenté a une faible ductilité par rapport aux métaux, ce qui signifie qu'il a une capacité limitée à se déformer plastiquement sans se casser. Cela peut provoquer des fissures ou des fractures dans l'outil ou la pièce à usiner s'il est soumis à une force ou à un impact excessif.
Sélection de meules pour le meulage de tiges de carbure cémenté
Le meulage est un processus consistant à enlever de la matière d'une pièce à usiner à l'aide d'un outil abrasif (tel qu'une meule) qui tourne à grande vitesse. Le meulage peut atteindre une précision, une finition de surface et une tolérance dimensionnelle élevées pour la pièce. Cependant, le meulage génère également de la chaleur, des frictions et des vibrations qui peuvent endommager la pièce ou l'outil.
Broyage cimenté tiges de carbure est particulièrement difficile en raison de leur dureté élevée et de leur faible conductivité thermique. Donc,
le choix de la meule est très critique pour obtenir de bons résultats de meulage.
La meule est composée de grains abrasifs (tels que le diamant ou le nitrure de bore cubique), de matériaux liants (tels que le métal ou la résine) et de pores (espaces entre les grains). Les grains abrasifs sont chargés de couper ou d’enlever de la matière de la pièce. Le matériau liant maintient les grains ensemble et détermine la résistance et la forme de la roue. Les pores permettent au liquide de refroidissement de circuler à travers la roue et d'évacuer la chaleur et les copeaux.
Les principaux facteurs à prendre en compte lors de la sélection d'une meule pour ciment tiges de carbure sont:
– Type abrasif : Le type d’abrasif doit correspondre à la dureté et à la ténacité du matériau de la pièce à usiner. Pour cimenté tiges de carbure,
Le diamant est l'abrasif le plus couramment utilisé car il a la dureté la plus élevée (10 sur l'échelle de Mohs) et peut couper n'importe quel matériau. Le nitrure de bore cubique (CBN) est une autre option qui a une dureté légèrement inférieure (9 sur l'échelle de Mohs) mais une stabilité thermique plus élevée que le diamant. Le CBN peut être utilisé pour broyer des carbures cémentés à haute teneur en cobalt ou avec des additifs de titane ou de tantale.
– Type de liant : le type de liant doit correspondre aux conditions et exigences de meulage. Pour cimenté tiges de carbure, les liants métalliques et résineux sont les plus couramment utilisés. Les liants métalliques ont une résistance et une rigidité élevées, ce qui permet de maintenir fermement les grains abrasifs et de maintenir la forme de la meule. Les liants métalliques conviennent au meulage grossier, au meulage intensif ou au meulage à grande vitesse. Les liants résineux ont une faible résistance et rigidité, ce qui peut permettre aux grains abrasifs de s'auto-affûter et de se détacher facilement. Les liants résine conviennent au meulage fin, au meulage de précision ou au meulage à basse vitesse.
– Taille des grains : La taille des grains détermine l’efficacité de coupe et l’état de surface du meulage. La taille des grains est mesurée par le nombre de mailles, qui indique le nombre d'ouvertures par pouce linéaire dans un tamis pouvant laisser passer les grains. Plus le nombre de mailles est élevé, plus la taille des grains est petite. Pour cimenté tiges de carbure, la taille typique des grains varie de 80 à 400 mesh. Une granulométrie plus petite peut produire une finition de surface plus lisse mais une efficacité de coupe inférieure. Une granulométrie plus grande peut produire une finition de surface plus rugueuse mais une efficacité de coupe plus élevée.
– Forme de la meule : La forme de la meule détermine la surface de contact et la pression entre la meule et la pièce à usiner. La forme de la roue est classée par un code standard composé d'une lettre et d'un chiffre. La lettre indique la forme de base de la roue, comme A (droit), B (cylindrique), D (coupe), etc. Le chiffre indique le profil spécifique de la roue, comme 1 (plat), 2 (concave). , 3 (convexe), etc. Pour cimenté tiges de carbure, les formes de roue typiques sont A1 (plat droit), D1 (cuvette plate) ou D6 (cuvette évasée).
En prenant comme exemple la fraise en bout de spécification D6, la sélection de meule courante est présentée dans le tableau 1.
Processus de broyage | Meule |
---|---|
Meulage de flûte | Diamant à liant métallique D6A2, maille 150/200 |
Broyage d'entailles | Diamant à liant métallique D1A1, maille 150/200 |
Meulage de dégagement | Diamant à liant métallique D6A2, maille 150/200 |
Meulage de face d'extrémité | Diamant à liant résine D6A2 150/200 mesh |
Méthodes de refroidissement pour le meulage des tiges de carbure cémenté
Le refroidissement est un élément essentiel du meulage car il peut prévenir ou réduire les dommages causés par la chaleur à la pièce ou à l'outil. Le refroidissement peut également améliorer l’efficacité de coupe, la finition de surface et la précision dimensionnelle de la pièce.
Le refroidissement peut être obtenu en utilisant un liquide de refroidissement, qui est un liquide ou un gaz qui circule à travers ou autour de la zone de broyage pour éliminer la chaleur et les copeaux. Le liquide de refroidissement peut également lubrifier et protéger la pièce et l'outil de la corrosion ou de l'oxydation.
Les principaux facteurs à prendre en compte lors de la sélection d'un liquide de refroidissement pour le meulage de tiges en carbure cémenté sont :
– Type de liquide de refroidissement : Le type de liquide de refroidissement doit correspondre au matériau de la pièce à usiner et aux conditions de meulage. Pour cimenté tiges de carbure,
Les liquides de refroidissement à base d'eau sont préférés aux liquides de refroidissement à base d'huile car ils offrent de meilleures performances de refroidissement, une viscosité plus faible, un coût inférieur et un impact environnemental moindre. Les liquides de refroidissement à base d'eau peuvent être de l'eau pure ou de l'eau mélangée à des additifs, tels que des huiles synthétiques, des émulsions ou des solutions. Les additifs peuvent améliorer les propriétés lubrifiantes, stables, anticorrosion, antirouille ou antimousse du liquide de refroidissement.
– Température du liquide de refroidissement : La température du liquide de refroidissement doit être suffisamment basse pour évacuer efficacement la chaleur, mais pas trop basse pour provoquer un choc thermique ou de la condensation sur la pièce ou l'outil. Pour les tiges en carbure cémenté, tiges de carbure,
la température optimale du liquide de refroidissement varie de 15°C à 25°C.
– Pression du liquide de refroidissement : La pression du liquide de refroidissement doit être suffisamment élevée pour pénétrer dans la zone de meulage et chasser les copeaux mais pas trop élevée pour provoquer des éclaboussures ou une érosion sur la pièce ou l'outil. Pour les tiges en carbure cémenté, tiges de carbure,
la pression optimale du liquide de refroidissement varie de 0,5 MPa à 2 MPa.
– Débit du liquide de refroidissement : le débit du liquide de refroidissement doit être suffisant pour couvrir toute la zone de broyage et fournir un refroidissement suffisant, mais pas excessif pour gaspiller le liquide de refroidissement ou causer des problèmes environnementaux. Pour les tiges en carbure cémenté, tiges de carbure,
le débit optimal du liquide de refroidissement varie de 5 L/min à 20 L/min.
– Position d'injection du liquide de refroidissement : La position d'injection du liquide de refroidissement doit être proche de la zone de meulage et alignée avec la direction de
la rotation de la roue et le mouvement d'avance. Cela peut garantir que le liquide de refroidissement atteint la zone de coupe rapidement et efficacement et n'interfère pas avec
l'évacuation des copeaux ou créer des bulles d'air.
Il est suggéré que lors du meulage de la rainure des copeaux de l'outil, la position d'injection du liquide de refroidissement soit indiquée sur la figure 1.
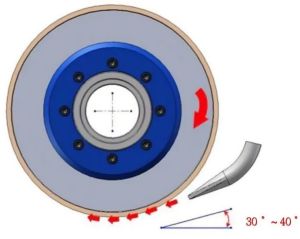
Conclusion
Broyage cimenté tiges de carbure est un processus difficile mais gratifiant qui peut produire des produits de haute qualité outils de coupe avec d'excellentes performances et durabilité. Cependant, cela nécessite une attention particulière