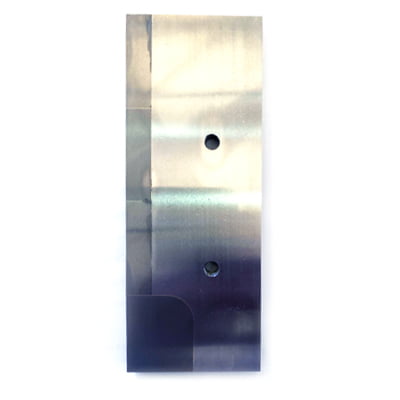
Contenido sobre soldadura de carburo de tungsteno
1. Problemas encontrados durante la soldadura fuerte con carburo de tungsteno
La soldabilidad del carburo de tungsteno es relativamente pobre. Esto se debe a su alto contenido de carbono, ya que las superficies sin limpiar suelen contener carbono libre, lo que dificulta la humectación del metal de aporte. Además, el carburo de tungsteno tiende a oxidarse a temperaturas de soldadura fuerte, formando una capa de óxido que afecta aún más las características de humectación del metal de aporte. Por lo tanto, la limpieza de la superficie antes de la soldadura fuerte es crucial para mejorar la humectabilidad del metal de aporte sobre el carburo de tungsteno. Cuando sea necesario, se pueden aplicar recubrimientos como cobre o níquel antes de la soldadura fuerte para mejorar el rendimiento de la unión.
2. Preparación de la superficie antes de la soldadura fuerte
Es esencial eliminar completamente los contaminantes de la superficie de las piezas de trabajo antes de soldar., incluidos óxidos, grasa, suciedad y pintura. Sin una limpieza adecuada, el metal de relleno fundido no puede humedecer adecuadamente la superficie del componente ni puede rellenar los huecos de las uniones. En ciertos casos, también puede ser necesario recubrir previamente las piezas con una capa de metal específica para mejorar la soldabilidad del material base y aumentar la resistencia a la corrosión de la unión soldada.
(1) Eliminación de contaminantes del aceite
Los contaminantes del aceite se pueden eliminar utilizando disolventes orgánicos como alcohol, tetracloruro de carbono, gasolina, tricloroetileno, dicloroetano y tricloroetano. Para la producción de lotes pequeños, los componentes se pueden sumergir en disolventes orgánicos para una limpieza profunda. En la producción de lotes grandes, el método más común es el desengrasado con vapor. Además, también se puede lograr un desengrasado eficaz en soluciones alcalinas calentadas; por ejemplo, sumergiendo las piezas de acero en una solución de sosa cáustica 10% a 70–80 °C.
(2) Eliminación de óxidos
Los óxidos en la superficie de las piezas antes de la soldadura fuerte se pueden eliminar mediante métodos mecánicos, grabado químico o grabado electroquímico. Los métodos mecánicos pueden incluir limas, cepillos de alambre, papel de lija, muelas abrasivas y chorro de arena para eliminar las películas de óxido. Las limas y el papel de lija se utilizan normalmente para la producción de piezas individuales, ya que crean ranuras ventajosas para la humectación y la distribución del metal de relleno. Para la producción en lotes, las lijadoras, los cepillos de alambre y los métodos de chorro de arena son más eficientes. Los métodos de limpieza mecánica no son adecuados para las aleaciones de aluminio y de titanio.
(3) Recubrimiento del material base con metal
La aplicación de un revestimiento metálico sobre la superficie del material base tiene como objetivo principal mejorar la capacidad de soldadura de ciertos materiales y mejorar la humectabilidad del metal de relleno. Este proceso también puede evitar interacciones adversas entre el material base y el metal de relleno que podrían degradar la calidad de la unión, como la formación de grietas o el desarrollo de compuestos intermetálicos frágiles. También puede servir como capa de relleno para simplificar el montaje y mejorar la productividad.
3. Materiales para soldadura fuerte
(1) Metales de relleno
Los metales de aporte más comunes incluyen cobre puro, aleaciones de cobre y zinc y aleaciones de plata y cobre. El cobre puro ofrece una excelente humectabilidad con varios materiales de carburo de tungsteno, pero debe soldarse en una atmósfera reductora de hidrógeno para lograr resultados óptimos. Sin embargo, debido a la alta temperatura de soldadura, la tensión térmica resultante en las uniones puede aumentar la probabilidad de agrietamiento. Las uniones soldadas con cobre puro tradicionales tienen una resistencia al corte de aproximadamente 150 MPa, con una ductilidad bastante alta, pero no son adecuadas para aplicaciones de alta temperatura.
Los rellenos de cobre y zinc son los más utilizados para soldar carburo de tungsteno y aceros para herramientas. Para mejorar la capacidad de humectación y la resistencia de la unión, a menudo se agregan elementos de aleación como Mn, Ni y Fe. Por ejemplo, en B-Cu58ZnMn, con un contenido de manganeso de aproximadamente 4 wt%, la resistencia al corte de la unión soldada con carburo de tungsteno puede alcanzar 300-320 MPa a temperatura ambiente, manteniendo 220-240 MPa a 320 °C. Agregar una pequeña cantidad de cobalto a B-Cu58ZnMn puede elevar la resistencia al corte a 350 MPa y, al mismo tiempo, proporcionar una mayor tenacidad al impacto y resistencia a la fatiga, lo que extiende significativamente la vida útil de herramientas de corte y brocas para perforación de rocas.
Los rellenos de plata y cobre tienen un punto de fusión más bajo, lo que da como resultado una tensión térmica mínima y una menor tendencia al agrietamiento durante la soldadura fuerte con carburo de tungsteno. Para mejorar la humectabilidad y aumentar la resistencia de la unión y las temperaturas de funcionamiento, se incorporan comúnmente elementos de aleación como Mn y Ni. Por ejemplo, los rellenos B-Ag50CuZnCdNi muestran una excelente humectabilidad con carburo de tungsteno y brindan un rendimiento general deseable para las uniones soldadas.
Para aplicaciones por encima de los 500 °C con altas exigencias de resistencia de las uniones, se pueden seleccionar rellenos a base de manganeso y níquel, como B-Mn50NiCuCrCo y B-Ni75CrSiB. Para la soldadura fuerte de acero de alta velocidad se requieren materiales de relleno específicos que coincidan con las temperaturas de temple, que se dividen en dos categorías: rellenos a base de hierro-manganeso compuestos principalmente de hierro-manganeso y bórax, que generalmente producen una resistencia al corte de alrededor de 100 MPa, aunque estas uniones son propensas a agrietarse. La otra categoría comprende aleaciones especiales de cobre que contienen Ni, Fe, Mn y Si, que minimizan las tendencias al agrietamiento y logran resistencias al corte de hasta 300 MPa.
(2) Flujos y gases protectores
La selección del fundente debe estar en consonancia con el material base y el metal de aporte elegido. Para la soldadura fuerte de aceros para herramientas y carburo de tungsteno, los fundentes principales que se utilizan son el bórax y el ácido bórico, a menudo complementados con diversos fluoruros (KF, NaF, CaF2, etc.). Los rellenos de cobre y zinc suelen combinarse con fundentes FB301, FB302 y FB105, mientras que los rellenos de plata y cobre pueden utilizar fundentes FB101 a FB104. Cuando se utilizan rellenos especiales para la soldadura fuerte de acero de alta velocidad, se emplean predominantemente fundentes de bórax.
Para evitar la oxidación del acero de herramientas durante el proceso de calentamiento y eliminar la limpieza posterior a la soldadura, se puede utilizar soldadura con protección de gas. Los gases protectores pueden ser gases inertes o reductores, con el requisito de que el punto de rocío del gas sea inferior a -40 °C. El carburo de tungsteno se puede soldar con protección de hidrógeno, lo que requiere un punto de rocío de hidrógeno inferior a -59 °C.
4. Procesos de soldadura fuerte
La soldadura fuerte de aceros al carbono para herramientas requiere una limpieza cuidadosa de la superficie, y las superficies mecánicas no necesitan ser demasiado lisas, ya que esto ayuda a la humectación y distribución de los materiales y el fundente. La superficie del carburo de tungsteno generalmente requiere chorro de arena o pulido con carburo de silicio o ruedas de diamante para eliminar el exceso de carbono y lograr una mejor humectación por parte del metal de relleno. El carburo de tungsteno y titanio presenta desafíos en cuanto a la humectación; por lo tanto, la aplicación de una pasta de óxido de cobre o níquel a su superficie y el calentamiento en una atmósfera reductora promueven una humectabilidad efectiva.
La soldadura fuerte de aceros al carbono para herramientas se realiza mejor antes del temple o simultáneamente con este proceso. Si la soldadura fuerte se realiza antes del temple, la temperatura de solidificación del metal de aporte debe superar el rango de la temperatura de temple, asegurando que las piezas unidas conserven suficiente resistencia cuando se recalienten a temperaturas de temple. Cuando la soldadura fuerte y el temple se realizan simultáneamente, se debe seleccionar un metal de aporte con una temperatura de solidificación cercana a la temperatura de temple.
La gama de composición de los aceros para herramientas de aleación es amplia, lo que requiere selecciones de metales de relleno y procesos de tratamiento térmico específicos según el tipo de acero particular para lograr un rendimiento óptimo de la unión.
En el caso del acero de alta velocidad, la temperatura de temple generalmente supera las temperaturas de fusión de los rellenos de plata-cobre y cobre-cinc, por lo que es necesario un temple previo. La soldadura fuerte se puede realizar durante el templado secundario o posteriormente. Si se requiere un temple posterior a la soldadura fuerte, solo se deben utilizar los rellenos especializados mencionados anteriormente. Al soldar herramientas de acero de alta velocidad, el uso de un horno de coque puede ser bastante eficaz; después de que se derrita el relleno, se debe retirar la herramienta de corte, se debe presionar el exceso de relleno y luego someterla a un temple en aceite, seguido de un templado a 550–570 °C.
Al soldar hojas de carburo de tungsteno a cuerpos de herramientas de acero, se deben emplear métodos como aumentar el espacio en la costura de soldadura y agregar una cuña compensatoria de plástico, junto con un enfriamiento lento posterior a la soldadura para reducir las tensiones térmicas y evitar la formación de grietas, extendiendo así la vida útil del conjunto de herramientas de corte de carburo de tungsteno.
5. Limpieza posterior a la soldadura fuerte
Los residuos de fundentes pueden ser corrosivos para las uniones soldadas y dificultar la inspección de la unión, por lo que deben eliminarse por completo. Inicialmente, el fundente residual en las piezas de trabajo se puede enjuagar con agua caliente o una mezcla general para eliminar fundentes, seguido de un tratamiento con soluciones de limpieza ácidas adecuadas para eliminar la capa de óxido del material base. Es fundamental evitar el uso de soluciones de ácido nítrico para prevenir la corrosión del metal soldado. Los residuos de fundentes blandos orgánicos se pueden limpiar con solventes como gasolina, alcohol o acetona, mientras que los residuos corrosivos como el óxido de zinc y el cloruro de amonio se deben limpiar en una solución de NaOH 10%, seguido de un enjuague con agua caliente o fría. Los residuos de fundentes de bórax y ácido bórico generalmente se pueden resolver utilizando métodos mecánicos o ebullición prolongada en agua.
6. Inspección de la calidad de la soldadura fuerte
Los métodos de inspección de uniones soldadas se pueden dividir en pruebas no destructivas y pruebas destructivas. A continuación se destacan los métodos de inspección no destructivos:
- Inspección visual
- Pruebas de fluorescencia y de líquidos penetrantes:Estos métodos permiten principalmente la detección de pequeñas grietas, porosidad u otros defectos que pueden no ser visibles mediante la inspección visual.
Este análisis exhaustivo enfatiza los problemas críticos y las soluciones en la soldadura fuerte con carburo de tungsteno, ayudando a comprender y mejorar el rendimiento y la calidad general de la unión.