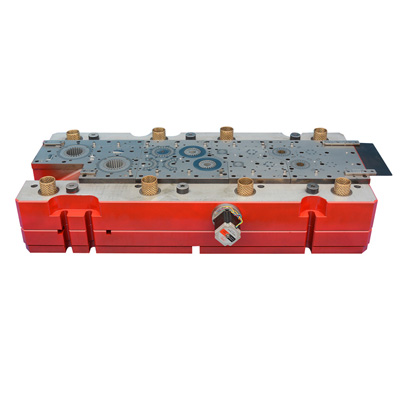
Structural Features of Stamping Die for Motor Stator and Rotor Iron Core
Stamping die technology for motor stator and rotor core is a high-tech that integrates stamping equipment, stamping dies, die materials and manufacturing processes. The stator and rotor iron core parts of the motor adopt multi-station progressive die, which has high precision, high efficiency and long service life.
The stamping process is that after the strip comes out of the roll, it is leveled by a leveling machine, and then fed by an active feeding device. After the strip enters the stamping die, the processes of blanking, forming, finishing, trimming, and active lamination of the iron core can be completed.
The stamping speed of the stator and rotor iron core progressive die of the motor is generally 200 to 600 times/min (SPM), and most of them work within the range of medium-speed stamping.
The main parts of the progressive die, the punch and the concave die, are made of Cemented Carbide Materials, which can be punched more than 1.5 million times each time the cutting edge is sharpened, and the total life of the die is more than 150 million times.
The high-speed precision punching machine has advanced design structure and high manufacturing precision. It is suitable for high-speed stamping of multi-station carbide progressive die, and can greatly improve the service life of progressive die.
The main structural features of the progressive die for the stator and rotor core of the motor are:
1. The dies adopts a double guide structure, that is, the upper and lower dies bases are guided by more than four large ball-type guide posts, and each discharge device and the upper and lower dies bases are guided by four small guide posts to ensure the mold has reliable guiding accuracy;
2. From the technical consideration of convenient manufacturing, testing, maintenance and assembly, the diesmold sheet adopts more block structure and combined structure;
3. In addition to the common structures of progressive dies, such as step guide system, discharge system (consisting of the main body of the stripper and split type stripper), material guide system and safety system (misfeed detection device), there are The special structure of the progressive die of the motor iron core: such as the counting and separating device for the automatic lamination of the iron core (that is, the pulling plate structure device), the riveting point structure of the punched iron core, the ejector pin structure of the iron core blanking and riveting point, the punching piece Tightening structure, twisting or turning device, safety device for large turning, etc. for blanking and riveting;
4. Since the main parts of the progressive die are usually made of hard alloys, the punch and the die are made of cemented carbide. Considering the processing characteristics and the price of the material, the punch adopts a plate-type fixed structure, and the cavity adopts a mosaic structure, which is convenient for assembly. and replacement.
Through the introduction of the above four points, people can fully understand the structure of the modern stator and rotor iron core stamping die of the motor, choose the iron core more conveniently, and improve the efficiency.
At present, our company’s motor stator and rotor core stamping die technology is mainly reflected in the following aspects:
1. The overall structure of the stator and rotor iron core progressive die of the motor (including double guide device, unloading device, material guide device, step guide device, limit device, safety detection device, etc.);
2. Structural form of core stacking riveting point;
3. The progressive die is equipped with automatic stacking riveting technology, skewing and rotating technology;
4. The dimensional accuracy and core fastness of the punched core;
5. The manufacturing accuracy and inlay accuracy of the main parts on the progressive die;
6. The degree of selection of standard parts on the dies;
7. Selection of materials for main parts on the dies;
8. Processing equipment for the main parts of the dies.
With the continuous development of motor varieties, innovation and the update of assembly process, the requirements for the accuracy of the motor iron core are getting higher and higher, which puts forward higher technical requirements for the progressive die of the motor iron core. The development trend is:
1. The innovation of die structure should become the development direction of modern stamping die technology for motor stator and rotor core;
2. The overall level of stamping dies is developing towards ultra-high precision and higher technology;
3. Innovative development of motor stator and rotor iron core with large slewing and twisted oblique riveting technology;
4. The stamping die for the stator and rotor core of the motor is developing in the direction of stamping technology with multiple layouts, no overlapping edges and less overlapping edges;
5. With the continuous development of high-speed precision punching technology, the dies should be suitable for the needs of higher punching speed.
The use of modern stamping die technology to manufacture the stator and rotor cores of the motor can greatly improve the level of motor manufacturing technology, especially in automotive motors, precision stepping motors, small precision DC motors and AC motors, which not only guarantees These motors have high technical performance and are suitable for the needs of mass production.
In addition, it must also be seen that in addition to modern stamping die manufacturing equipment, that is, precision machining machine tools, modern stamping dies for designing and manufacturing motor stator and rotor cores must also have a group of practically experienced design and manufacturing personnel. This is manufacturing The key to precision stamping dies. With the internationalization of the manufacturing industry, China’s stamping die industry is rapidly integrating with international standards, and improving the specialization of die products is an inevitable trend in the development of the die manufacturing industry, especially in today’s rapid development of modern stamping technology, motor stator and rotor core parts. Modern stamping technology will be widely used.