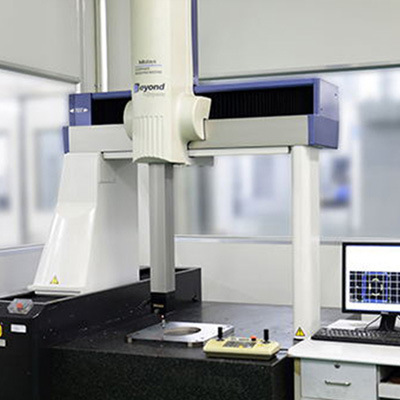
– Introduction:
Cemented carbide is a composite material made of hard carbide particles bonded together by a metal matrix, usually cobalt. It is one of the most versatile and durable materials for cutting, drilling, and wear-resistant applications in various industries, such as metalworking, mining, aerospace, automotive, and construction. However, not all cemented carbide products are created equal. Depending on your specific needs and challenges, you may require custom cemented carbide solutions that are tailored to your exact specifications and preferences. In this article, we will show you how custom cemented carbide solutions can help you achieve optimal performance, quality, and efficiency in your operations.
– Carbide Grades:
One of the most important aspects of customizing cemented carbide solutions is choosing the right carbide grade for your application. Carbide grades are classified according to their grain size, which affects their hardness, toughness, wear resistance, and corrosion resistance. Generally speaking, finer-grained carbides have higher hardness and wear resistance, but lower toughness and corrosion resistance than coarser-grained carbides. Mixed-grained carbides combine the properties of both fine and coarse grains to achieve a balance of performance characteristics. For example, if you need a cemented carbide product for high-speed machining of steel or cast iron, you may opt for a fine-grained carbide grade that can withstand high temperatures and abrasion. On the other hand, if you need a cemented carbide product for impact-resistant applications such as rock drilling or mining tools, you may choose a coarse-grained carbide grade that can resist cracking and chipping. By working with a reputable cemented carbide manufacturer or supplier, you can select the best carbide grade for your specific needs and challenges.
– Shapes:
Another important aspect of customizing cemented carbide solutions is choosing the right shape for your product. Cemented carbide products come in various shapes, such as rods, bars, strips, plates, discs, rings, blocks, and special forms. Each shape has its own advantages and disadvantages in terms of performance and functionality. For example, rods are commonly used for making cutting tools such as drills, end mills, reamers, and taps. Bars are often used for making wear parts such as guides, bushings, nozzles, and valves. Strips are suitable for making knives, blades, scrapers, and saws. Plates are ideal for making dies, molds, punches, and inserts. Discs are used for making circular saws, slitting cutters, and milling cutters. Rings are used for making bearings, seals, gaskets, and washers. Blocks are used for making large components such as anvils, hammers, rollers, and cylinders. Special forms are used for making complex or irregular shapes that cannot be made by standard shapes. By working with a reputable cemented carbide manufacturer or supplier,
you can customize the shape of your product to fit your specific geometry and dimension requirements.
– Dimensional Tolerances:
A third important aspect of customizing cemented carbide solutions is ensuring the right dimensional tolerances for your product. Dimensional tolerances are the allowable variations in the dimensions of a product that do not affect its functionality or quality. Dimensional tolerances are crucial for high-precision and high-quality applications that require tight fitment and alignment between components. Dimensional tolerances are influenced by several factors, such as sintering shrinkage, grinding accuracy, and measurement methods.
Sintering shrinkage is the reduction in size that occurs when the green compact (the unsintered mixture of carbide powder and binder) is heated to a high temperature to form the final product.
Grinding accuracy is the degree of precision that can be achieved by grinding the product to its final shape and size.
Measurement methods are the techniques and instruments used to measure the dimensions of the product.
By working with a reputable cemented carbide manufacturer or supplier,
you can ensure that your product meets your desired dimensional tolerances
and avoid any problems or defects that may arise from dimensional variations.
– Delivery:
A final important aspect of customizing cemented carbide solutions is ensuring timely and reliable delivery of your product to your location. Delivery options and services vary depending on the cemented carbide manufacturer or supplier you choose to work with. Some factors that affect delivery include delivery methods, delivery time, delivery cost, and delivery quality.
Delivery methods are the ways in which your product is transported from the manufacturer or supplier to your location,
such as express shipping, air freight, sea freight, or rail transport.
Delivery time is the duration between placing your order and receiving your product at your location.
Delivery cost is the amount of money you pay for the delivery service
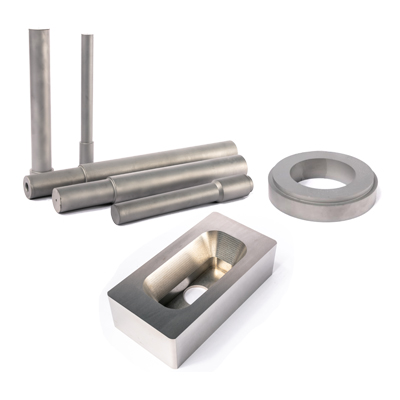