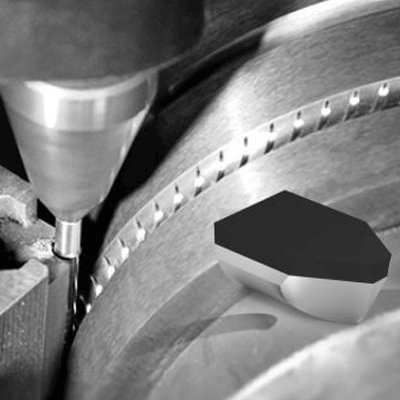
Carbide Roller Ring Manufacturing, Turning and Grinding
Usually carbide roller rings are available in special grades, which are also composed of tungsten carbide and binder.
Since the rollers are used in high temperature, shock and corrosive production environments, our technicians have developed carbide grades for rollers with high cobalt + nickel, tantalum and niobium for its application.
How to manufacture carbide roller rings by powder metallurgy?
In the first step, the various powders such as tungsten carbide powder, cobalt powder, nickel, (paraffin or PEG) are first mixed and then wet ground.
In the second step, the mixed powders are dried and pressed with a die, and the large size roller ring needs to be pressed with a 2000 ton press.
In the third step, we need to trim the pressed blanks, I can put the groove shape I want at this time and process it. Because the hardness HRA of carbide is not very high at this time, it is more suitable for processing.
The third step, then after low-pressure sintering furnace 1450 ℃ high temperature sintering 48 hours, after sintering it will reach the hardness of HRA70-90.
In the fourth step, the roller ring will be ground and machined by using diamond grinding wheel or PCD/PCB tool.
1) Turning carbide rolls and roll rings
Roller ring processing methods, there are turning and then grinding; there is a direct grinding molding, without turning, especially steel mills to repair carbide rolls are generally direct grinding-based, grinding and then according to the need to process the thread groove and lettering.
Roll ring turning tool selection: generally the roll hardness is different, the hole type slot is different, the material of the selected tool is also different, generally the roll ring turning below HRA90 choose PCBN inserts; while the roll turning above HRA90, choose higher hardness diamond tools or use resin bond diamond grinding wheel for grinding.
2) Imitation processing of tungsten steel rolls and roll rings
For the processing of hole-type grooves above R3, grinding wheels can be used for direct grinding, or diamond tools can be used for profiling (such as chamfering process and grooving and other shaping processes can choose custom diamond tools).
Cutting instead of grinding, which can improve the processing efficiency and the carbide chips of cutting method are easier to recover.
Because the customization of forming grinding wheel needs cycle time or needs mold, but the customization cycle of non-standard forming tools is faster, so the cutting method is more conducive to improve the production cycle time.
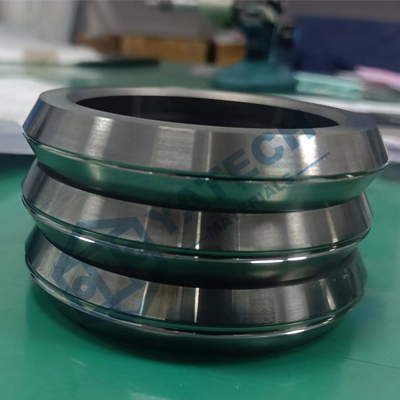
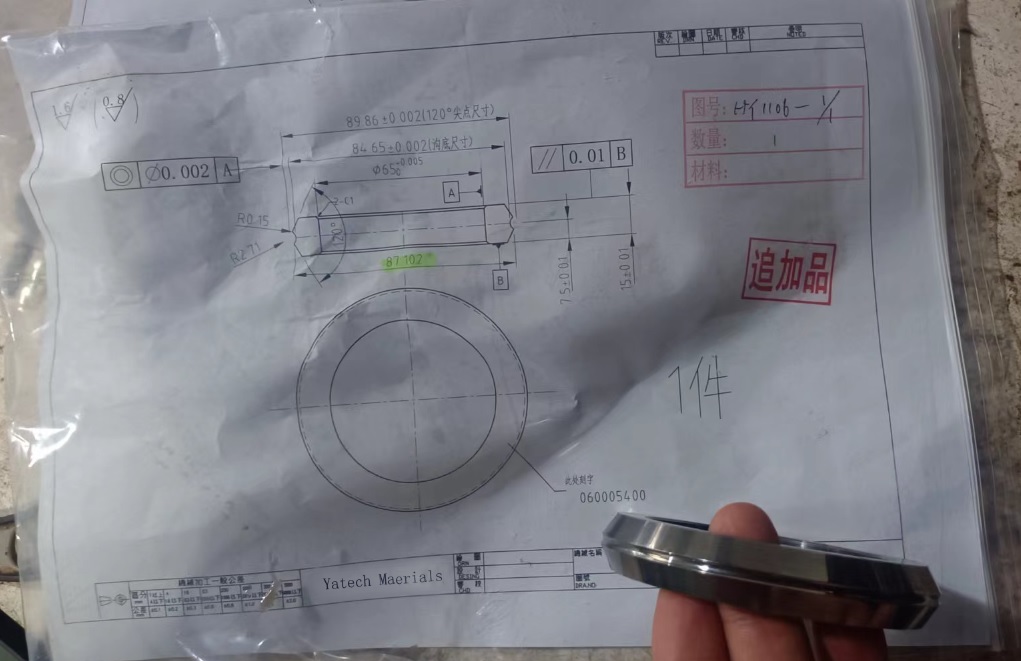