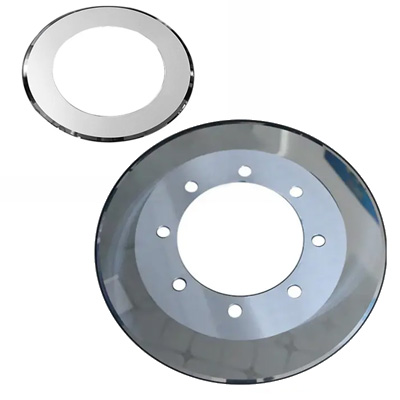
Carbide circular blades, Thin circular blades, fiberglass cutting blades, optical fiber cutting blades
Applications of circular cutting blades
With the development of science and technology, the emergence of various characteristics of fine packaging products, disposable paper products and non-woven products more and more, processing and cutting these tools is carbide circular blades (carbide slitting knife), corrugated paper carbide circular cutter.
The rapid development of the new energy industry, lithium battery carbide slitting round blade, pole piece copper foil aluminum foil carbide round knife, for the new energy industry to provide efficient and durable cutting solutions.
The increased demand for medical protective and personal hygiene products affected by Corona Virus Disease 2019, COVID-19, meltblown fabric cutting requirements require efficient cutters, which carbide meltblown fabric slitting large round knives can easily solve.
Material of circular slitting blade
Traditional circular cutters are made of steel material, through traditional metallurgy, casting, forging into material, and then through heat treatment and machining forming, the process is complex and costly, and the service life is about 1 million times when the normal working speed is increased to 600 rpm. And the service life of carbide cutter at 1500 rpm can reach 40-50 million times, for carbide disc cutter, efficiency and life are its advantages, reduce the risk of downtime and product quality fluctuations.
For carbide disc cutter process improvement and improvement, is the premise of batch to market. Carbide disc cutter requires high material hardness and wear resistance. The wear resistance and hardness of carbide are related to the tungsten carbide grain size and cobalt content. The finer the tungsten carbide grain size and the lower the cobalt content, the higher the hardness and wear resistance.
Yatech Materials’ material experts can easily solve the problem of material toughness by using the following formula with tungsten carbide grain size of 0.6~0.8μm, cobalt content of 10% and inhibitor of 0.5%. mixture (RTP), can be perfect for the problem of toughness.
Tungsten carbide disc slitting tool
Carbide disc cutter size specifications are numerous, D10-400*d2-300*T170.1-25mm, the rib height of the edge requires consistent, to avoid the impact and wear to the bearing due to dynamic balance problems during high-speed rotary cutting.
How to eliminate the radial ellipticity and axial taper of the sintered blanks is a difficult problem.
The solution is to place a graphite core in the inner cavity of the carbide circular cutter blank during sintering to prevent the graphite core and carbide from reacting and coating into a layer of AL2O3 powder.
This is only possible after precise calculation and repeated experiments, otherwise, either the graphite core does not work there is a gap or the interference is too large and cracks occur in the carbide. Since the shrinkage coefficient of the powder is related to the purity and density, and the shrinkage coefficient parallel to the grain and perpendicular to the grain is very different, and the heating and cooling of the two during the sintering process are not consistent, it is more difficult to do accurate calculation.
Nowadays, we mainly use the method of loading furnace symmetry, that is, the workpiece blank is placed in the position of the base in the furnace to ensure that the outer circle of the workpiece blank and the annular heating body are on the concentric circle. In this way, the radial ellipticity and axial taper of the sintered blanks of the carbide cutter are less than 0.3%.
While the edge ribs of steel circular cutters are EDM machined, carbide must be powder metallurgically produced to produce high precision size ribs to ensure no defects.
Advantages of carbide circular slitting cutter
The internal metallurgical organization of carbide round cutting blade products is dense, avoiding the phenomenon of chipping of the cutting edge in the process of fine grinding and use, improving the finish of the cutting section and the requirements of one cutting and forming; using high-precision grinding machine to fine grind the cutting edge, high processing accuracy, high finish to mirror effect, sharp edge, the cut section is flat, smooth, no pitting; high hardness, sharp edge, good wear resistance, one Long work cycle of cutting machine, more than 10 times the life of high-speed steel slitting blade, by the subsequent treatment of coating carbide round slice is dozens or even hundreds of times the high-speed steel slitting blade; acid resistance, alkali resistance, corrosion resistance, oxidation resistance, rust-free, adapt to a variety of production cutting environment.
Our company’s standardized custom production, standardized production process and strict quality control of the perfect combination of stable product quality, especially for long cutting operations, to eliminate your worries.