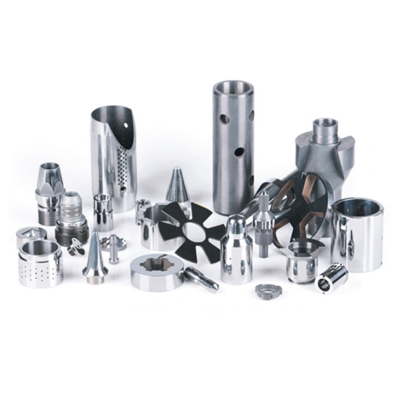
Tungsten carbide wear parts have become increasingly popular in various industries due to their numerous advantages over traditional materials. Yatech, a leading manufacturer in the field of tungsten carbide wear parts, has extensive manufacturing experience and capability in producing high-quality wear parts for various applications.
Advantages of Tungsten Carbide Wear Parts
Tungsten carbide wear parts are known for their exceptional hardness and resistance to wear, corrosion, and impact. These wear parts are made by mixing tungsten carbide powder with a binder material, which is typically cobalt or nickel. The resulting material is then shaped using various manufacturing techniques such as pressing, sintering, and machining. The benefits of tungsten carbide wear parts include:
- High wear resistance: Tungsten carbide wear parts are incredibly durable and can withstand heavy usage without showing any signs of wear or deformation. This makes them ideal for use in high-wear applications such as mining, drilling, and construction.
- Corrosion resistance: Tungsten carbide wear parts are highly resistant to corrosion, making them an excellent choice for use in harsh environments where traditional materials would quickly degrade.
- High toughness: Tungsten carbide wear parts are tough and can withstand heavy impact without breaking or chipping. This makes them ideal for use in applications that involve high impact and shock loads.
Main Applications of Tungsten Carbide Wear Parts
The main applications of tungsten carbide wear parts are found in industries such as mining, oil and gas, construction, and agriculture. Some specific applications include:
- Mining: Tungsten carbide wear parts are used in mining equipment such as drill bits, cutting tools, and crusher parts. These wear parts are highly resistant to wear and can withstand the abrasive and harsh conditions found in mining operations.
- Oil and gas: Tungsten carbide wear parts are used in the oil and gas industry for drilling equipment, such as drill bits, stabilizers, and fishing tools. These wear parts are designed to withstand the high-temperature and high-pressure conditions found in oil and gas wells.
- Construction: Tungsten carbide wear parts are used in construction equipment such as trenchers, paving machines, and demolition tools. These wear parts are designed to withstand the harsh conditions found on construction sites and provide long-lasting performance.
- Agriculture: Tungsten carbide wear parts are used in agricultural equipment such as plows, cultivators, and harrows. These wear parts are designed to withstand the abrasive conditions found in soil and provide long-lasting performance.
Expertise in Tungsten Carbide Wear Parts
Yatech has extensive experience and capability in the manufacturing of tungsten carbide wear parts. We have a highly skilled team of engineers and technicians who can design and manufacture wear parts to meet the specific requirements of their clients. Yatech uses advanced manufacturing techniques to produce high-quality wear parts that provide excellent performance and durability.
In conclusion, tungsten carbide wear parts offer many advantages over traditional materials, making them an ideal choice for use in high-wear, high-impact, and harsh environments. Yatech’s expertise in the manufacturing of tungsten carbide wear parts makes them a trusted partner for clients in various industries who require high-quality, long-lasting wear parts.
Comparison of Cemented Carbide and Tool Steel Properties
Property | Cemented Carbide | Tool Steel |
---|---|---|
Hardness | Very high | High |
Wear resistance | Very high | High |
Toughness | Low to moderate | High |
Corrosion resistance | Good to excellent | Poor |
Thermal conductivity | Low | High |
Coefficient of thermal expansion | Low | High |
Density | High | Medium to high |