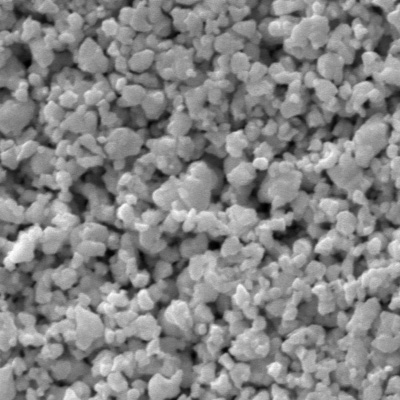
One brand corresponds to many qualities, that is, to the different needs of different customers. How to make powder products that satisfy customers?
Whether the powder index requirements are the same, the process is the same?
1. Tungsten carbide (WC) powder concept:
Tungsten carbide powder is the main raw material for the production of cemented carbide, the chemical formula is WC. It is a black hexagonal crystal with a hardness similar to that of diamond, and is a good conductor of electricity and heat. The melting point is between 2600°C and 2870°C, the boiling point is 6000°C, and the relative density is 15.77g/cm3. WC is insoluble in water, hydrochloric acid and sulfuric acid, but easily soluble in the mixed acid of nitric acid and hydrofluoric acid. It can be dissolved in various carbides, especially in titanium carbide, and has a high solubility, forming a TiC-WC solid solution.
In terms of surface color: the WC of coarse particles is gray with obvious metallic luster, the WC of medium particles is gray, the WC of fine particles is dark gray, and the WC of ultra-fine particles is black.
Tungsten carbide powder production equipment
1. Carbon Dispensing Equipment – Stirrer
1) Components
It is mainly composed of high-speed motor (30KW), agitator cavity (320L), stirring paddle, pressure relief and dust suction pipe, circulating water cooling system and N2 protection pipe. The ratio of the diameter of the motor pulley to the shaft pulley determines the actual speed of the stirring paddle.
2) Working principle:
After the electric hoist is used to hoist the tungsten powder and carbon black mixture into the stainless steel cavity of the mixer according to the mixing weight requirements, the motor rotates the stirring paddle in the cavity at a high speed through the belt drive, so that the material can move randomly in multiple dimensions in the cavity. Then mix evenly.
3) Process parameters
Carbon content + dopant content + stirring time
Carbon allocation is the key, how to accurately release the carbon allocation process?
2. Carbon Dispensing Equipment – Mixer
1) Components
It is composed of mixing cone, transmission motor, gear box, axis fish bone and bracket.
2) Working principle:
Through the motor to the transmission, it is transmitted to the bearing to make the double-cone bucket turn over, so as to achieve the effect of mixing the materials evenly. The function of the axis fishbone is to stir and disperse, so that the materials will not stick and mix more evenly.
2) Process parameters
Carbon content + dopant content + mixing time
3. Carbonization equipment – carbon tube furnace
1) Components
Furnace head feeding end (preheating section) + furnace body (heating belt) + furnace tail (water cooling section) + boat push mechanism (push rod, motor, chain gear box, stroke in-position alarm device and frequency regulator) + pipeline (H2 , N2, circulating cooling water) + heating system (copper sleeve, conductive flange, copper bar, transformer) + temperature control system (radiation thermometer, temperature controller and control cabinet)
2) Working principle:
Heating: The graphite cone is connected with the conductive copper sleeve, and the inner tube conducts heat through the close cooperation of the two
Carbonization: The carbonization process needs to be carried out under the protection of hydrogen in the furnace tube, because hydrogen has strong penetrating ability and reducing ability, it can reduce the oxide film on the surface of tungsten powder. 800 degrees Celsius) can interact with the carbon black in the charge to generate CH4, and CH4 decomposes at high temperature to decompose carbon with high activity and deposit on the surface of W powder. At high temperature of carbonization, the activity of W powder and carbon black increases. Black gradually diffuses into W powder and chemically forms WC
3) Process parameters
Temperature/Push Speed/Boat Loading/Gas Flow/Process Time
4. Carbonization screening equipment – ball mill
Working principle: power 9.2KW, volume 380L. The motor is connected to the connecting shaft to drive the cavity. After circulating water, the massive tungsten carbide material and the small alloy balls (including 12mm, 18mm, 25mm, 35mm) are loaded into the ball grinding drum according to a certain proportion, and the drum is at a certain speed. Rotate, so that the alloy ball in the cavity continuously hits the block material to achieve the purpose of material crushing.
Ball milling effect: The effect of ball mill crushing WC mainly depends on the movement state of alloy balls and materials, and the movement of balls and materials depends on the rotation speed of the ball mill cylinder. The movement of alloy balls and materials is divided into three situations:
a) Ball mill speed is too slow
b) The ball mill rotates properly
c) The ball mill rotates too fast
5. Carbonization screening equipment – screening machine
Purpose: The tungsten carbide ball milled into powder state is screened by appropriate sieves to remove impurities such as coarse particles, graphite fragments and waste alloy balls.
The working principle of the rotary vibrating screen: the power is 75KW, the motor is connected to the soft belt, and the eccentric block controls the material position of the screen tray. The powdery material is vibrated onto the sieve tray at a certain rate, and the sieve tray vibrates at a high speed through the rotation of the eccentric block. .
Principle of ultrasonic sieving: On the basis of the rotary vibrating screen, an ultrasonic generator is added to the sieve tray. The principle of ultrasonic application for sieving is that the high-frequency oscillation signal sent by the ultrasonic generator is converted into high-frequency mechanical oscillation by the transducer and propagated to the screen. The fine-grained powder on the net vibrates under the action of the sound field to generate shock waves, and at the same time, it is easier to penetrate the mesh of the screen under the action of vibration, so as to achieve the purpose of easy screening.
Process parameters: material weight/sieve mesh number
6. Carbonization sieving equipment – batch combiner
1) Working principle:
Through the motor to the transmission, the transmission to the bearing makes the double-cone barrel overturn, and the material moves back and forth to achieve the effect of mixing the material evenly.
2) Function: Mix materials in different small batches fully to achieve a more uniform and stable material quality.
3) Process parameters:
RPM/Time/Weight