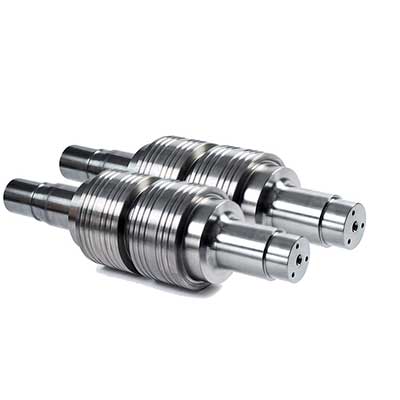
Drawing design requirements for changing cast iron rolls to carbide rolls
1. Drawings of cast iron rolls (preferably electronic versions such as CAD).
2. The maximum and minimum diameter of the outer diameter of the roller.
3. The distance from both ends to the first groove (the installation distance of the guide roller).
4. Groove size.
5. The maximum size of the inner hole of the sealing ring.
6. Type of rolled steel: round steel or threaded roll.
7. Whether the thread roller is cut, if so, the distance of the cut.
Cemented carbide composite rolls have the advantages of good wear resistance, short roll change time, good surface quality of rolled materials, obvious negative tolerance effect, and low labor intensity in hot-rolled rebar and bar production, especially in slit rolling. It can ensure the uniformity of the split rolling, the stability of the strip shape, reduce the number of slot changes, and improve the efficiency of the rolling mill. Therefore, the promotion of the use of carbide composite rolls from the K4 stands and later stands is immeasurable to improve the production potential.
Countries all over the world use it as a replacement for traditional cast iron rolls to update carbide composite rolls to improve rolling stock quality and reduce costs.
Countries all over the world use it as a replacement for traditional cast iron rolls to update carbide composite rolls to improve rolling stock quality and reduce costs.